Harnessing Artificial Intelligence and Predictive Maintenance to Revolutionise Plant Reliability and Operational Efficiency
- Automate Asia Magazine
- Jun 5
- 4 min read
An exclusive interview with Dr. Deny Sapian, Head of Bearings & Industrial Solutions at Schaeffler Malaysia on maximising cost and efficiency within the manufacturing landscape.

Dr. Deny Sapian is currently responsible for Industrial Sales and Business Development at Schaeffler in Malaysia. His professional journey is marked by experiences across multiple sectors, including plant operations, O&M engineering services, and construction in the oil and gas, power generation, manufacturing, and OEM.
With over 25 years of hands-on experience in plant commissioning, operations and rotating equipment start-ups & maintenance, Dr. Deny Sapian’s expertise has helped him to identify emerging industry needs and address challenges faced by plant operators and maintenance professionals. He has also helped to bridge knowledge gaps in plant operations and fostered practical strategies for optimizing plant performance while maximising returns on investment.

1. Can you provide a brief history of Schaeffler and its presence in Malaysia?
Schaeffler has been driving forward inventions and developments in the field of motion technology for over 75 years. From the revolutionary cage-guided needle roller bearings to mechanical and mechatronics solutions for industrial and automotive sectors, Schaeffler has been actively supporting its customers across a wide range of motion technology. In 1995, Schaeffler expanded its footprint to Malaysia where we remain invested.
Given the complex and rapidly changing landscape in Malaysia, Schaeffler prioritises digitalisation, innovation and sustainability within our business operations and solutions to expand our position as an innovative, reliable, and agile partner in an increasingly competitive environment.
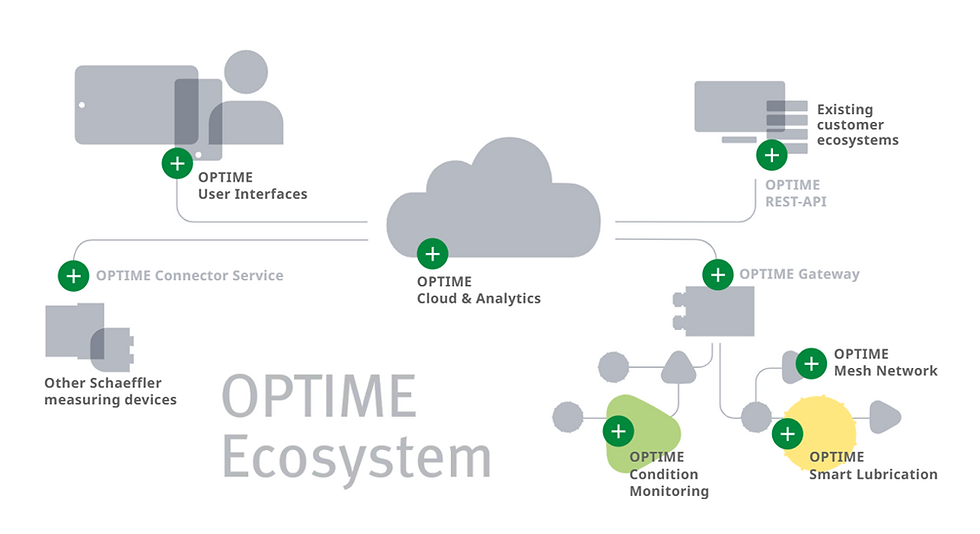
2. How does Schaeffler ensure the quality and reliability of its unique blend of high precision motion engineering related products and solutions?
Quality assurance is directly integrated into the manufacturing process at Schaeffler and is supported by regular audits. Additionally, Schaeffler has also received ISO certifications like ISO 9001:2015 and IATF16949 among many others, that reflect our strong adherence to international standards.
We have defined worldwide standards for occupational safety and environmentally friendly manufacturing. Our suppliers have also undergone rigorous assessment and monitoring to ensure that they meet Schaeffler’s quality standards.

3. How does the company contribute to the integration of digital transformation in smart manufacturing in Malaysia and globally?
As a leader in motion technology, Schaeffler is driving the future of smart manufacturing. Our comprehensive solutions within the bearings and industrial solutions have helped our partners in Malaysia and across the world to improve operational efficiency within their productions.
Using a combination of a trifecta of smart sensors, AI analysis, and Schaeffler’s deep expertise, our OPTIME Ecosystem delivers highly accurate predictive maintenance. The technology analyses vibration, temperature, and load data to forecast multistratal rotating equipment failures weeks in advance. By leveraging machine learning and AI algorithms built on our extensive physical model library, OPTIME Ecosystem identifies potential issues with pinpoint accuracy, preventing costly disruptions.
Schaeffler’s contribution extends beyond offering an innovative solution in condition monitoring. Our Industrial Lifetime Solutions portfolio represents a proactive cost-saving strategy that empowers plant operators to navigate the complexities of Industry 4.0 and beyond. All of these translate to reduction of unplanned downtime, optimization of maintenance intervals, enhancing equipment performance, and lowering maintenance costs. Furthermore, the shift toward digitalized plant operations has also proven to improve work safety and operational reliability.

4. What are some of the major challenges in implementing predictive maintenance, and how can these challenges be overcome?
Two challenges stand out: data quality and model validation – the twin titans of predictive maintenance challenges. The principle “garbage in, garbage out” is all too familiar, and a sophisticated model loses its value if it foresees non-existent failures. This is where Schaeffler’s strategic approach becomes crucial. Our OPTIME Ecosystem offers more than just sensors; it combines Schaeffler’s expertise in the field of bearing technology, vibration analysis, and profound knowledge on rotating machine characteristics and lubrication to deliver accurate and reliable data.
Additionally, the lack of resources and budget constraints often hinder companies from implementing predictive maintenance. However, the reality is that investing in predictive maintenance is not an option but a necessity. While budget concerns are valid, the long-term savings and enhanced operational efficiency far outweigh the initial investment
Schaeffler’s Approach:
Our focus is on driving strategic transformation. While there is an upfront cost, the cost-savings from reduced downtime will optimise maintenance and improve energy efficiency, ultimately offering a substantial ROI for our partners.

The Customer’s Perspective:
Initial cost concerns are valid, but the hidden costs of inefficiency can be even more detrimental. Predictive maintenance enhances operations beyond fixing machines — it boosts safety, efficiency, and competitiveness, turning maintenance into a profit driver. In essence, overcoming these challenges requires a partnership. Schaeffler collaborates with its customers and partners to transform data into actionable insights, resulting in reduced downtime, optimised maintenance, and a more efficient plant to pave the way for smarter manufacturing.
5. The manufacturing landscape is constantly evolving. From your perspective, what are the key trends we should watch out for in the next few years, and how is Schaeffler positioning itself to stay ahead?
Increasing digitalisation, automation and a shortage of skilled labour in production is expected to increase capital expenditures on plant and equipment. Likewise, the introduction of stricter safety standards and a heightened focus on sustainability across the supply chain will drive manufacturers to look at innovative solutions to drive productivity and efficiency across multiple industries.
Our expertise in motion technology allows us to provide a comprehensive portfolio, which ranges from individual components such as sensor-enabled bearings through to complex mechatronic systems, that are well positioned to support manufacturers to generate efficiency increases.
The portfolio is rounded out by solutions for preventive maintenance such as sensor-based condition monitoring and intelligent lubrication. For instance, our OPTIME Ecosystem which is built on deep bearing knowledge and advanced analytics facilitates remote and autonomous operations, thereby increasing machine life cycles, resulting in energy efficiency and reliable operations.
Furthermore, Schaeffler also offers expert and remanufacturing services that extend machine lifetime that help to reduce operating costs and lower carbon emissions.